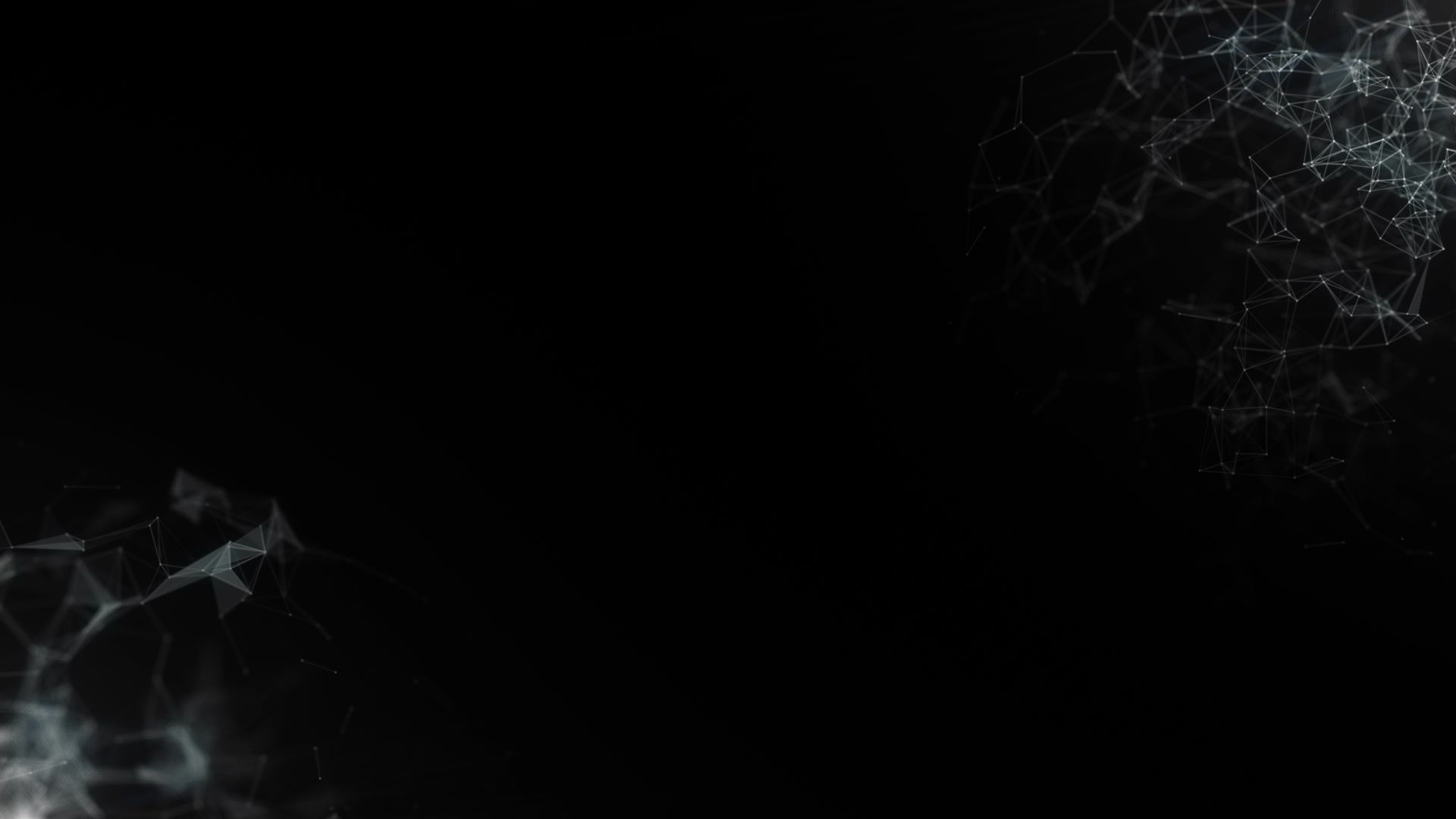
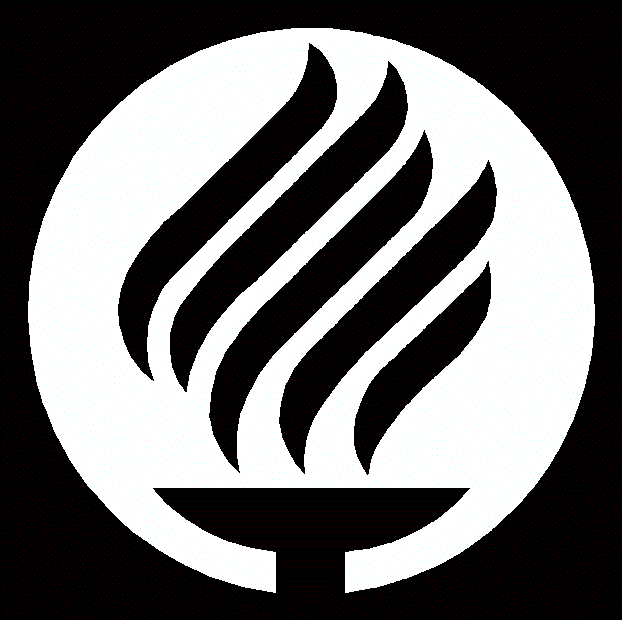
Proyecto Redes Industriales
MR2019.2 Ma-Vi 17:30-19:00
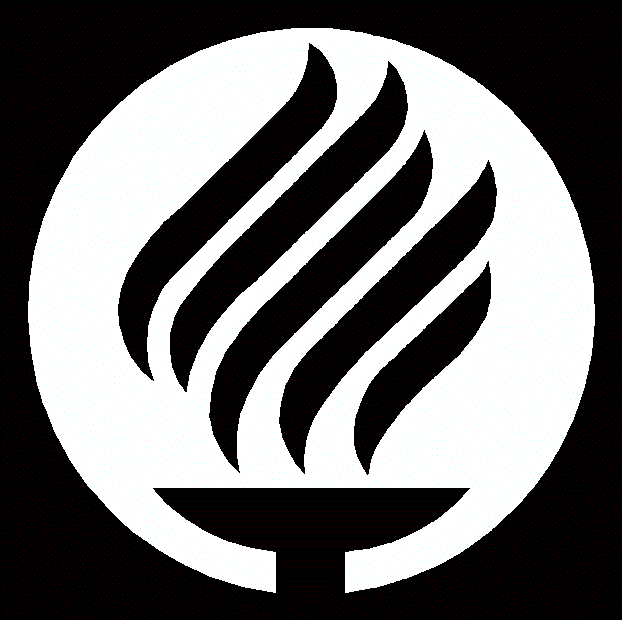
Introducción y Configuración de PLC´s
Resumen
En esta práctica se realizó la configuración de un PLC S7-300 Siemens para generar una secuencia sencilla con ayuda de la estación electro-neumática.
Se configura la conexión Pc-PLC, se realizan ajustes en el software STEP 7, se hace la configuración electro-neumática y se carga el programa para poder correrlo.
Objetivos
-
Conocer las características, el funcionamiento y la configuración del PLC S7-300.
-
Familiarizarse con el equipo del laboratorio y recordar el uso de las estaciones electro-neumáticas.
-
Recordar los métodos de programación.
-
Aprender algunos comandos básicos y la manera de utilizar el software Step 7.
Material
-
PLC S7-300.
-
12 Pares de cable banana-banana.
-
4 Sensores de final de carrera.
-
6 Mangueras.
-
2 Electroválvulas 5/2.
-
2 Pistones de doble efecto.
-
Botonera.
Marco Teórico
Un Controlador Lógico Programable es una computadora industrial diseñada específicamente para recibir señales de una operación y dispositivos de campo y, por medio de un programa almacenado, generar señales de salida para controlar máquinas o procesos. Esta computadora cuenta con características especiales en cuanto en el diseño de su unidad central de procesamiento (CPU) y de sus módulos de entrada y salida (módulos I/O). Los PLCs son utilizados para el control de procesos automáticos de producción.
Diagrama de proceso.
Un Controlador Lógico Programable es una computadora industrial diseñada específicamente para recibir señales de púlpitos de operación y dispositivos de campo y, por medio de un programa almacenado, generar señales de salida para controlar máquinas o procesos. Esta computadora cuenta con características especiales en cuanto en el diseño de su unidad central de procesamiento (CPU) y de sus módulos de entrada y salida (módulos I/O). Los PLCs son utilizados para el control de procesos automáticos de producción
PLC SIMATIC S7-300
El SIMATIC S7-300 es un sistema de automatización universal, principalmente para los sectores industriales. Permite una solución óptima para aplicaciones en arquitecturas de control.
PLC S7-300.
Los componentes del PLC son:
CPU: Es el cerebro del sistema y es el que se encarga de tomar las decisiones en base a la aplicación programada.
I/O: Módulos para señales digitales y analogicas.
CP: Procesadores de comunicación entre hombre y máquina, se tiene procesadores de comunicación para conexiones a redes y para conexión punto a punto.
Fm: Sirven para operaciones de cálculo rápido.
SM: Adaptan la señales del proceso.
Los PLC cuentan con operaciones tales como:
-
Operaciones Básicas álgebra de Boole.
-
Operaciones Aritméticas.
-
Comparadores.
-
Transferencia de datos.
-
Temporizadores y contadores.
En STEP 7 se puede hacer uso de tres lenguajes de programación:
-
KOP (esquema de contactos): Este es un lenguaje gráfico que permite visualizar los programas en diagrama escalera.
-
AWL (lista de instrucciones): Este es un lenguaje orientado a máquinas. Este equivale a los pasos ordenados que realiza el CPU. Este lenguaje sería un lenguaje equivalente al lenguaje ensamblador.
-
FUP (Diagrama de funciones): Este lenguaje es también un lenguaje visual que permite la programación en diagramas de algebra booleana.
Lenguajes.
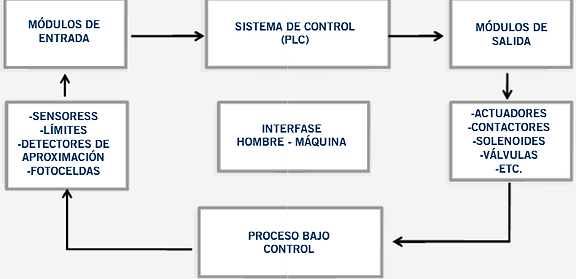


Desarrollo
Configuración de la red local con la PC
Para que el PLC y la PC funcionen adecuadamente se requiere que ambos estén conectados a la misma red de Ethernet, para esto se necesita comprobar o configurar la dirección IP.
Como primer paso se necesita ir al panel de control como lo muestra la imagen 1.1
Imagen 1.1
El siguiente paso es abrir Redes e Internet como se muestra en la imagen 1.2
Imagen 1.2
A Continuación se requiere seleccionar “Cambiar configuración del adaptador” como se muestra en la imagen 1.3
Imagen 1.3
Como siguiente paso se necesita hacer click derecho en “Conexion de area local” y seleccionar “propiedades” como muestra la imagen 1.4
Imagen 1.4
Como siguiente paso hay que seleccionar el protocolo de internet dependiendo de cual indique el PLC, tal como se muestra en la imagen 1.5
Imagen 1.5
Como último paso se necesita ingresar la dirección IP y la máscara de subred, los cuales se pueden encontrar en las etiquetas como se muestra en la imagen 1.6
Imagen 1.6
Programación con Administrador SIMATIC 7
Como primer paso una vez que abramos el programa SIMATIC 7 se va abrir una ventana donde nos dice la introducción el cual podemos hacer caso omiso y hacer click en cancelar, tal y como se muestra en la imagen 2.1
Imagen 2.1
Para poder comenzar tenemos que seleccionar archivo y nos posicionamos en “Nuevo” para hacerle doble click, mostrado en la imagen 2.2
Imagen 2.2
Se abrirá una ventana donde podremos indicar el nombre del proyecto y el lugar donde queremos guardar el archivo en el cual se va a trabajar, una vez que indiquemos lo anterior hacemos click en el botón aceptar, tal y como lo muestra la imagen 2.3
Imagen 2.3

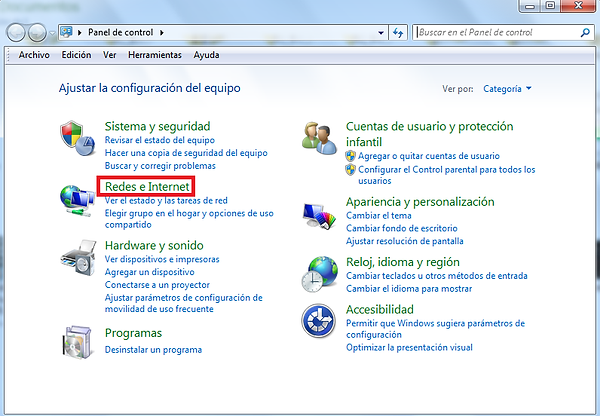

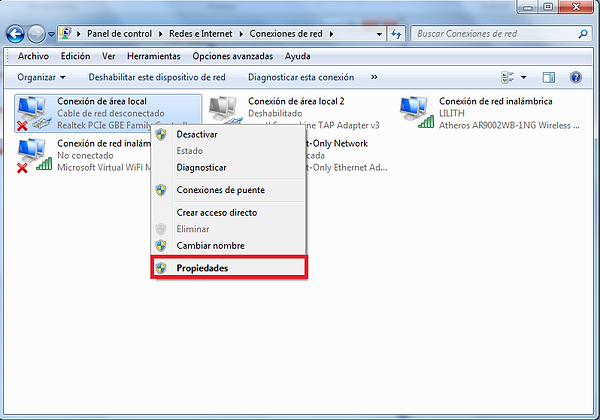



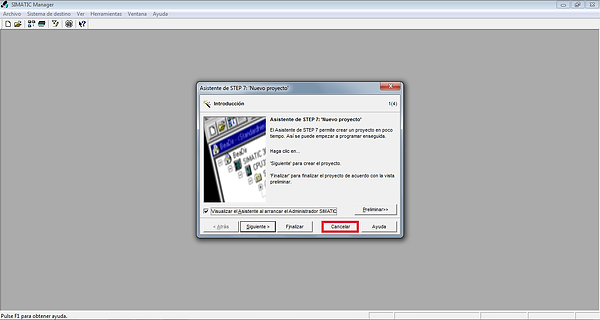
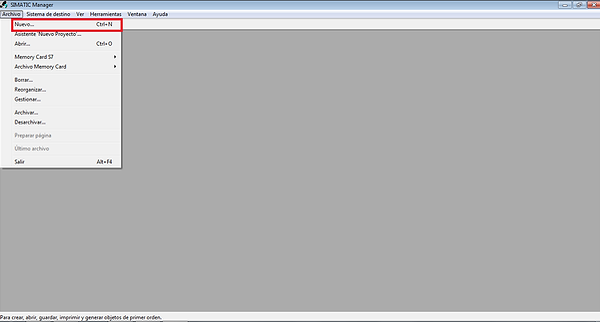

Una vez que ya se crea el archivo entonces le hacemos click izquierdo y nos colocamos en “Insertar nuevo objeto” para poder seleccionar el SIMATIC correspondiente, como se muestra en la imagen 2.4
Imagen 2.4
Como siguiente paso seleccionamos el SIMATIC que hayamos seleccionado y nos aparecerá el nombre de “Hardware” en la ventana derecha, le hacemos doble click en “hardware y nos enviara a otra ventana, en esta ventana hacemos click con el botón izquierdo y seleccionamos “insertar objeto” tal como se muestra en las imagenes 2.5 y 2.6
Imagen 2.5
Imagen 2.6
Una vez que se ha seleccionado “insertar objeto”, del lado derecho se seleccionan todos los módulos que se utilizarán para el control y manejo del PLC. Primero se empieza con la fuente de alimentación, seguido del CPU, DI (digital inputs), DO (digital outputs), CP y finalmente el puerto ETHERNET, viendo el controlador de frente sería de izquierda a derecha dejando el . Para poder darlos de alta es necesario conocer el módulo o familia de cada uno de ellos. Estos módulos se diferencían por un número de catálogo o de referencia el cual se encuentra escrito en los módulos físicamente, ya sea en la parte superior o inferior en letras blancas. Una vez que se conoce la referencia de cada módulo, esta referencia se busca en la ventana del lado derecho y se dan de alta. El único detalle que se tiene que tomar en cuenta es que al momento de dar de alta los módulos, se empiezan en el orden ya mencionado sólo que después del CPU se deja el espacio del perfil de soporte o riel del PLC, como se muestra en las imágenes 2.7,2.8 y 2.9.
Imagen 2.7 Imagen 2.8 Imagen 2.9
Una vez que se ha terminado con la configuración del hardware, se selecciona la opción del CPU que se haya dado de alta, que en nuestro caso fue el “CPU314C-2 PN/DP”. Después se abre la carpeta de “Programa”, “Bloques” y se selecciona OB1 como se muestra en la imagen 3.
Imagen 3.
En esta parte se comienza con la programación del código para la secuencia que ejecutará el controlador. En nuestro caso, la secuencia era A+ B+ B- A-. Teniendo como A al pistón 1 y B al pistón 2.
Este programa cuenta con diferentes maneras de programar, en nuestro caso programamos en escalera. Para esto primero dimos de alta los símbolos que utilizamos en el programa, para esto en la barra de “menú”, se selecciona la opción de “herramientas” y después “Tabla de símbolos” como se muestra en la figura 3.1. Ahí mismo se especifica el símbolo, dirección y tipo de dato como se muestra en la figura 3.2. En nuestro caso nosotros fijamos los pistones como DO (digital outputs), botón de marcha, de paro, sensores como DI (digital inputs) y las marcas.
Imagen 3.1
Imagen 3.2
Una vez que se crea la tabla de símbolos, se empieza a programas en los segmentos. Para esto se utilizan los contactos que se encuentran en la parte superior como se muestra en la imagen 3.3. Estos contactos pueden ser normalmente abiertos o normalmente cerrados. Y finalmente al final de cada segmento se finaliza con una bobina la cual se encuentra junto a los contactos en la barra de herramientas.
Los contadores, temporizadores y otras funciones se encuentran en la parte izquierda, para insertar un nuevo segmento se da click derecho sobre el segmento y se selecciona la opción de “Nuevo segmento”. Una vez que se termina la programación se da click en “Subir a módulo” que se encuentra en la parte superior, como se muestra en la figura 3.3.
Imagen 3.3
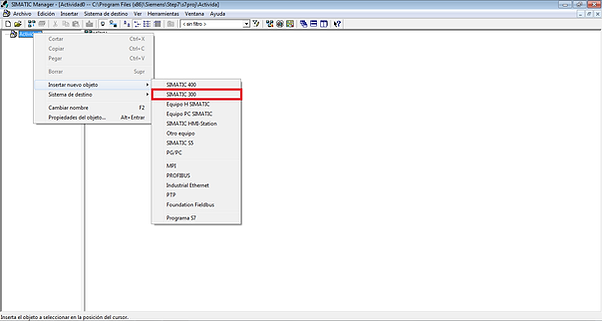

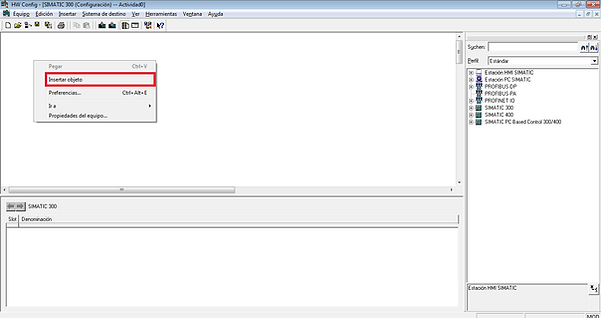





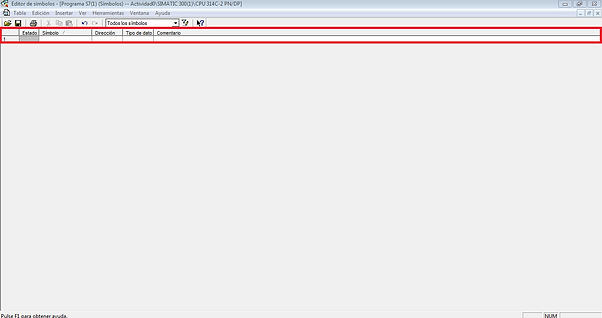

Resultados
Para la programación de la secuencia fue necesario utilizar una marca para que funcionara correctamente, se utilizó un contador y un temporizador “T1”.
La programación se basa principalmente en los pistones, Y1 mostrando el avance del pistón A, Y2 como el retroceso, Y3 el avance del pistón B y Y4 como el retroceso. SA0 se utilizó para denominar al primer sensor del pistón A en posición 0 y SA1 como el sensor para cuando A ha avanzado. Así igual SB0 y SB1 para el pistón B.
En la primer parte del código se programa una bobina “Mx” la cual se activa al presionar el botón de marcha “Bm”, la bobina del contador “Mp” y la de botón de paro “Bp” apagadas. Finalmente la retroalimentación de la bobina “Mx” en paralelo. Para que una vez presionado el botón de marcha, con la retroalimentación, se vuelva a activar la bobina.
En la siguiente parte del código, se programa la bobina de Y2 que es el retroceso del pistón A, la cual se activa al estar activada la marca de grupo 1 “MG1” y el sensor SB0 indicando que el pistón B está en posición 0, contraído
En el segmento 3 se programó la bobina de Y1 que es el avance del pistón A. Esta bobina se activa con los contactos SA0, SB0 y Mx activados, indicando que ambos pistones están en posición 0 y que se ha presionado el botón de marcha, pero teniendo el contacto de la marca de grupo 1 “MG1” desactivada.
En el segmento 4 se programó la bobina de Y3, que es el avance del pistón B. Para esto es necesario que el pistón A ya haya salido por lo que el contacto de “SA1” debe estar activado y la marca de grupo “MG1” desactivada.
Para activar la bobina de Y4, que indica el retroceso del pistón B, es necesario que la marca de grupo “MG1”, “SB1” y “Mt” estén activados. Indicando que la bobina del grupo 1 “MG1” ya se ha activado, la bobina del temporizador “Mt” y “SB1” indicando que el pistón B está fuera.
En el sexto segmento se programa la bobina del grupo 1 “MG1”, esta marca es la que sirve para saber en qué parte del código se encuentra. Esta marca se activa al estar “SB1” activado y “SA0” desactivado. Indicando que ambos pistones han avanzado.Y la retroalimentación de la misma bobina, para que cuando el pistón B retroceda, la marca siga activada.
En el siguiente segmento, se programó el contador con paso. Este cuenta cada vez que se activa la bobina de “Y2”, retroceso de A. Este contador transfiere los datos a “MW1” y se resetea con el botón de marcha “Bm”.
La programación de la bobina del contador “Mp” se realizó en el segmento 8. Aquí se programó el contador que recibe los datos de “MW1” y al ser iguales esos datos a 3, se activara. Esto quiere decir que el programa se ha completado 3 veces. Para esto se utilizó un contacto normalmente cerrado con un nombre “fantasma” esto quiere decir que al no existir esa contacto, y al estar el contacto normalmente cerrado, no necesita que se active ninguna bobina para que comience el funcionamiento del contador.
En el último segmento se programó la bobina del temporizador “Mt”, el cual se activa con “SB1”, esto quiere decir, cuando avanza el pistón B,y se resetea con “SA0”, cuando el pistón A retrocede.
Estas últimas funciones fueron necesarias porque se quería que una vez que el pistón B avanzara, se esperara 2 segundos y después retrocediera. Y el contador para que después de que el programa se corriera completo tres veces, se detuviera.
Video funcionamiento
Simulación Fluidsim


Conclusiones
Alejandro Islas. La práctica se realizó con éxito y se cumplio con los objetivos establecidos, ya que aprendimos cuál es el funcionamiento y la configuración del PLC, pero en específico el modelo S7-300.Comprendimos la lógica que se utiliza en el software Step 7, el cual es el enlace entre la PC y el PLC. Así que se obtuvo la secuencia correctamente a pesar de algunas dificultades que se presentaron.
Daniel Vega. El objetivo de esta práctica se cumplió ya que se conocieron las características y el funcionamiento del PLC S7-300, de igual manera se pudieron aprender ciertos comandos del software Step 7 los cuales consisten en poder comunicar la PC con el PLC mediante el IP. Se pudo programar con el lenguaje KOP por el método cascada para así poder comprender el orden que debe seguir y el saber poner las marcas para que los pistones funciones de acuerdo a la secuencia que se nos asignó.
Eduardo Chagoyan. La práctica nos llevó un poco de tiempo, ya que lo más tardado fue dar de alta los módulos y revisar que todo estuviera en orden con el controlador, como las direcciones, conexiones, etc. La programación no fue muy complicada, debido a que ya se había trabajado con un PLC anteriormente y no varía mucho. Podría decir que la práctica se realizó de la mejor manera, un poco tardado pero de forma exitosa. Se conoció el funcionamiento del controlador, la conexión con los módulos, el cargar el programa en el controlador y lo más importante el correcto funcionamiento de la secuencia.
Bibliografía
Programar con STEP 7. (2006, Marzo 1). Extraído Agosto 29, 2015, de https://cache.industry.siemens.com/dl/files/056/18652056/att_70833/v1/S7prv54_s.pdf.
Introducción y ejercicios prácticos. (2010, Mayo 1). Extraído Agosto 29, 2015, de https://cache.industry.siemens.com/dl/files/551/45531551/att_56646/v1/S7gs___d.pdf.
SIMATIC S7-300. (2003). Retrieved August 29, 2015, from http://upcommons.upc.edu/bitstream/handle/2099.1/4298/Simatic_S7_300_PLC.pdf?sequence=12&isAllowed=y.
Dorantes, D., Manzano, M., Sandoval , G., & Vásquez, V. (2008). Automatización y control. México: Mcgraw-hill.